Advanced Techniques in Steel Stamping for Precision Production
In the world of accuracy production, the development of metal stamping methods has actually been a crucial force in attaining unequaled degrees of precision and performance. As industries consistently require better resistances and intricate designs in their steel components, the mission for advanced techniques in metal marking has actually heightened. From the utilization of innovative multi-stage marking processes to the combination of sophisticated automation technologies, the landscape of steel marking is going through a profound makeover. In this vibrant field, the merging of technology and precision is improving the opportunities of what can be attained in steel construction.
Advanced Multi-Stage Stamping Processes
Discussing the intricacies of innovative multi-stage stamping processes reveals the innovative methods used in modern-day manufacturing practices. Metal Stamping. Multi-stage stamping is a complex procedure that involves multiple steps to transform a flat sheet of metal right into a final stamped product. The usage of modern dies, where different procedures are carried out at each phase of the marking procedure, enables for high precision and performance in the production of complex metal parts
Throughout the first stages of multi-stage marking, the flat metal sheet is fed right into the stamping press, where a series of dies are used to reduce and shape the material. Subsequent stages include extra forming, bending, and punching procedures to further fine-tune the component. Each phase is meticulously made to develop upon the previous one, bring about the production of intricate geometries with tight resistances.
Advanced multi-stage stamping procedures need a high level of knowledge and precision to guarantee the high quality and uniformity of the stamped parts. By utilizing innovative machinery and tooling, makers can generate a wide variety of metal parts with effectiveness and precision.
Precision Tooling Innovations
Precision tooling developments have transformed the steel marking sector, enhancing efficiency and high quality in producing procedures. These developments have actually significantly affected the means steel elements are generated, resulting in higher precision and consistency in the last items. One vital innovation is the advancement of computer system numerical control (CNC) innovation in tooling design and manufacture. CNC systems enable complex styles to be translated directly into tooling, ensuring precision and repeatability in the stamping procedure.
In addition, the integration of sensing units and real-time tracking abilities in accuracy tooling has actually made it possible for makers to discover and address concerns promptly, reducing downtime and minimizing scrap prices. By including wise modern technology into tooling, drivers can maximize specifications such as stress, rate, and placement throughout the marking operation, resulting in boosted product high quality and increased productivity.
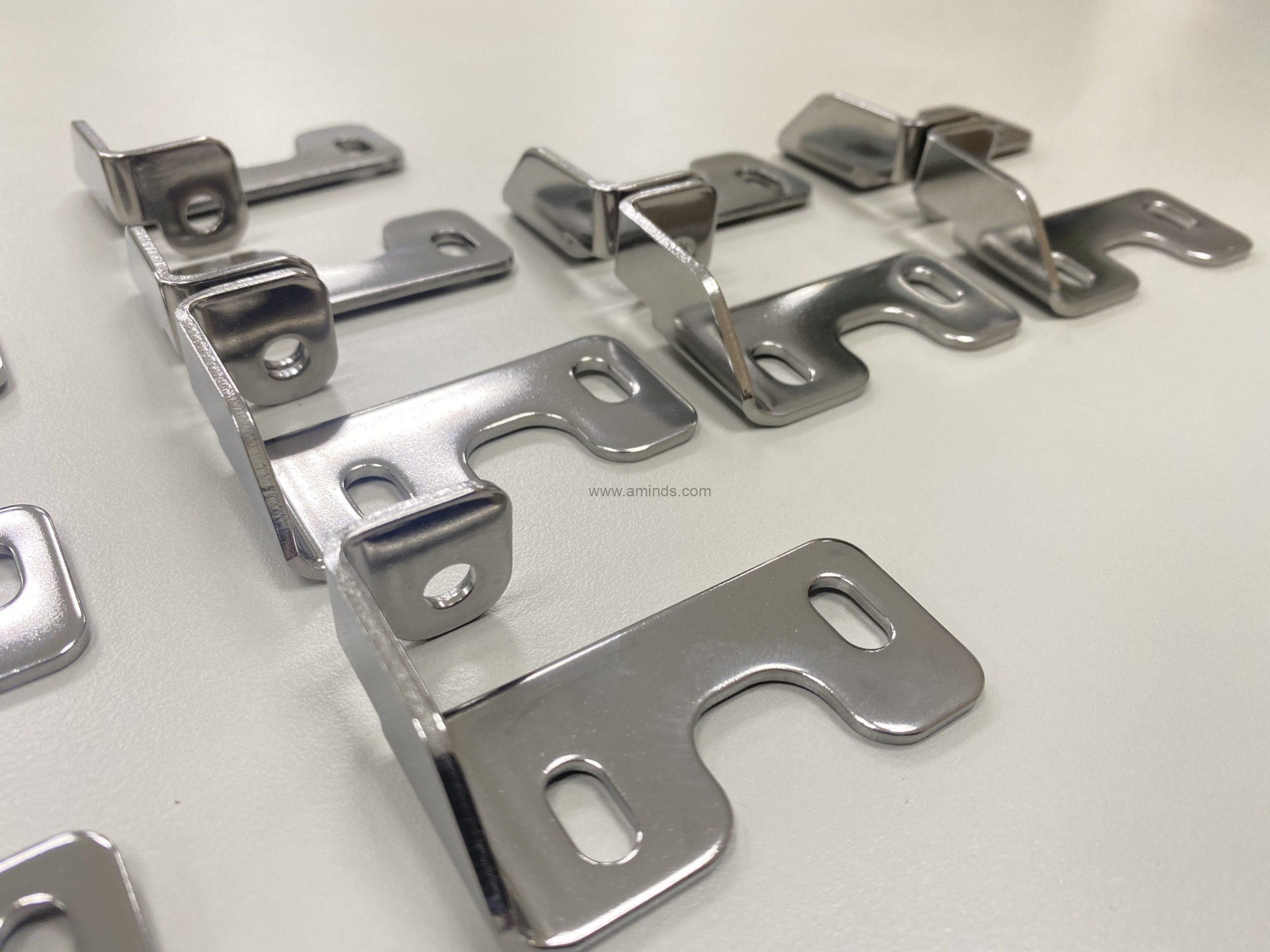
Automation in Metal Stamping
The evolution of accuracy tooling advancements in the steel stamping market has actually paved the way for significant improvements in automation, changing the production landscape in the direction of raised efficiency and efficiency. Metal Stamping. Automation in metal stamping entails the usage of innovative equipment and robotics to do numerous tasks typically accomplished by human operators. This shift in the direction of automation provides countless advantages, consisting of enhanced precision, faster manufacturing cycles, and lowered labor prices
One secret element of automation in metal stamping is the execution of computer mathematical control (CNC) systems, which allow accurate why not check here control over the marking process. CNC technology permits the development of facility and intricate steel get rid of regular high quality. Furthermore, automated systems can click this link be set to run constantly, bring about higher outcome rates and shorter preparations.
Moreover, automation enhances office safety and security by decreasing manual handling of hefty products and lessening the threat of mishaps (Metal Stamping). As producing sectors proceed to embrace automation, the future of metal marking holds fantastic assurance for also higher effectiveness and advancement
High-Speed Stamping Techniques
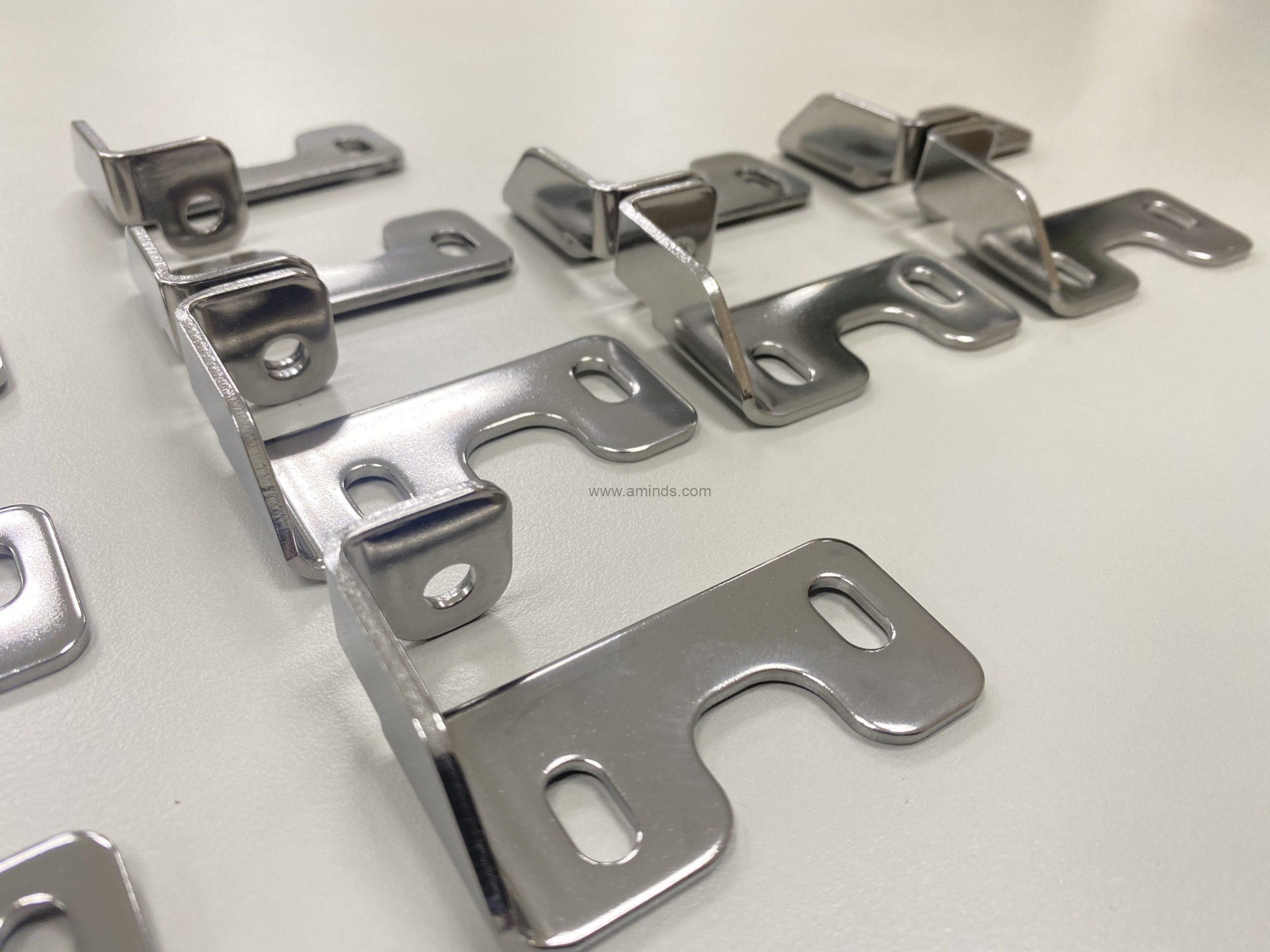
Among the key benefits of high-speed stamping methods is the ability to generate a huge quantity of parts in a shorter quantity of time compared to typical marking methods. This raised efficiency not only allows makers to meet tight manufacturing due dates but also allows expense savings with economies of range. Furthermore, high-speed marking can help in reducing product waste by optimizing the product usage throughout the stamping process.
Furthermore, high-speed stamping strategies often integrate innovative attributes such as quick die change systems and real-time surveillance abilities, additionally boosting the overall performance and flexibility of the steel marking procedure. As modern technology proceeds to breakthrough, high-speed stamping is expected to play an essential role in driving the future of precision production.
Top Quality Control in Stamping Operations
Effective top quality control measures are essential for ensuring the dependability and uniformity of steel stamping procedures. Quality control in marking operations entails a series of systematic procedures aimed at detecting and protecting against problems in the manufactured components. One essential facet of quality assurance in steel stamping is the usage of advanced evaluation techniques such as optical assessment systems and coordinate measuring makers (CMMs) to confirm the measurements and tolerances of stamped components.
In addition, quality assurance procedures in marking operations often consist of the application of analytical procedure control (copyright) approaches to monitor the manufacturing procedure in real-time and guarantee that it stays within appropriate restrictions. By examining data and identifying fads, producers can proactively address any type of variances from the wanted high quality requirements.
Additionally, quality assurance in steel marking procedures also involves complete product screening to guarantee that the raw materials made use of fulfill the called for requirements for the stamping process. This might consist of conducting product hardness tests, tensile strength examinations, and dimensional assessments to read this article guarantee the quality and honesty of the stamped parts. Generally, carrying out robust quality assurance actions is vital for accomplishing premium stamped components continually.
Conclusion
Finally, progressed strategies in steel stamping play an essential function in accuracy production procedures. Via multi-stage marking procedures, cutting-edge tooling remedies, automation, high-speed strategies, and rigorous top quality control measures, makers can attain higher degrees of accuracy and effectiveness in their operations. These advancements in metal marking innovation have enabled business to create intricate components with tight tolerances, inevitably resulting in enhanced item high quality and customer satisfaction in the production market.